Fast and Affordable Packaging Machine Repair Services You Can Rely On
Fast and Affordable Packaging Machine Repair Services You Can Rely On
Blog Article
Quick and Reliable Product Packaging Maker Repair Work Services to Decrease Downtime
In the affordable landscape of production, the effectiveness of packaging operations pivots on the integrity of machinery. Quick and trustworthy repair services are crucial in minimizing downtime, which can lead to significant monetary losses and functional troubles.
Relevance of Timely Repairs
Prompt repairs of packaging machines are crucial for maintaining functional performance and decreasing downtime. In the busy setting of manufacturing and product packaging, also minor malfunctions can lead to significant hold-ups and performance losses. Resolving concerns immediately guarantees that devices operate at their optimal ability, consequently securing the flow of operations.
In addition, normal and timely upkeep can avoid the escalation of small issues into significant malfunctions, which commonly incur greater repair service expenses and longer downtimes. A proactive technique to maker repair work not just protects the integrity of the tools however also boosts the general reliability of the assembly line.
Additionally, prompt repair services contribute to the long life of packaging equipment. Makers that are serviced without delay are less most likely to experience extreme deterioration, permitting services to maximize their financial investments. This is especially crucial in industries where high-speed product packaging is important, as the demand for consistent efficiency is paramount.
Benefits of Reliable Solution Suppliers
Reliable provider play an essential duty in guaranteeing the smooth procedure of packaging devices. Their proficiency not just boosts the efficiency of repair work yet also contributes substantially to the longevity of equipment. Trustworthy solution providers are geared up with the technological expertise and experience essential to diagnose issues precisely and carry out reliable solutions quickly. This minimizes the threat of recurring problems and guarantees that makers run at optimum efficiency degrees.

In addition, a reputable provider offers comprehensive support, consisting of training and advice for team on equipment procedure and upkeep finest methods. This not only empowers staff members yet additionally grows a culture of safety and efficiency within the company. On the whole, the advantages of engaging dependable company expand past instant repairs, favorably influencing the entire operational operations of packaging procedures.
Common Product Packaging Equipment Problems
In the world of packaging procedures, various problems can endanger the effectiveness and capability of machines (packaging machine repair). An additional common problem is misalignment, which can trigger jams and unequal packaging, affecting product Read Full Report top quality and throughput.
Electric problems can likewise interrupt packaging operations. Faulty electrical wiring or malfunctioning sensing units may cause erratic machine behavior, creating hold-ups and increased operational expenses. Additionally, software program glitches can hinder the equipment's programming, resulting in operational inadequacies.
Inconsistent item circulation is one more vital issue. This can occur from variants in item shape, weight, or size, which might impact the machine's capacity to manage items precisely. Insufficient training of operators can aggravate these problems, as inexperienced personnel may not identify early signs of malfunction or might abuse the equipment.
Addressing these usual packaging maker problems without delay is important to preserving performance and making sure a smooth procedure. Regular evaluations and navigate here proactive maintenance can substantially minimize these concerns, cultivating a trustworthy product packaging environment.
Tips for Minimizing Downtime
To minimize downtime in product packaging operations, carrying out a proactive upkeep method is critical. Consistently scheduled upkeep checks can identify possible problems prior to they escalate, making sure machines run successfully. Establishing a regimen that includes lubrication, calibration, and evaluation of vital parts can dramatically lower the regularity of unanticipated failures.
Educating team to operate equipment properly and acknowledge very early indication of malfunction can likewise play an important duty. Encouraging operators with the understanding to do standard troubleshooting can prevent small concerns from triggering significant hold-ups. Additionally, keeping a well-organized stock of crucial extra components can expedite fixings, as waiting on components can cause prolonged downtime.
In addition, documenting machine efficiency and maintenance activities can help determine patterns and reoccurring issues, permitting for targeted interventions. Integrating sophisticated surveillance innovations can supply real-time information, allowing predictive maintenance and lessening the threat of sudden failures.
Finally, promoting open communication in between operators and upkeep groups guarantees that any irregularities are quickly reported and attended to. By taking these proactive procedures, services can enhance functional efficiency and significantly reduce downtime in packaging processes.
Choosing the Right Repair Service Service
Selecting the ideal repair service for product packaging makers is a crucial decision that can considerably impact functional performance. An appropriate solution company guarantees that your equipment is repaired promptly, successfully, and to the highest requirements. Begin by reviewing the provider's experience with your details sort of product packaging devices. A professional acquainted with your machinery can identify issues much more accurately and apply remedies extra quickly.
Following, think about the company's track record. Seeking responses from other organizations within your market can offer insights into reliability and top quality. Certifications and partnerships with acknowledged tools manufacturers can additionally show a dedication to quality.
Furthermore, evaluate their reaction time and schedule. A company who can use prompt support lessens downtime and keeps production circulation constant. It's additionally vital to ask about warranty and service guarantees, which can show the confidence the provider has in their job.
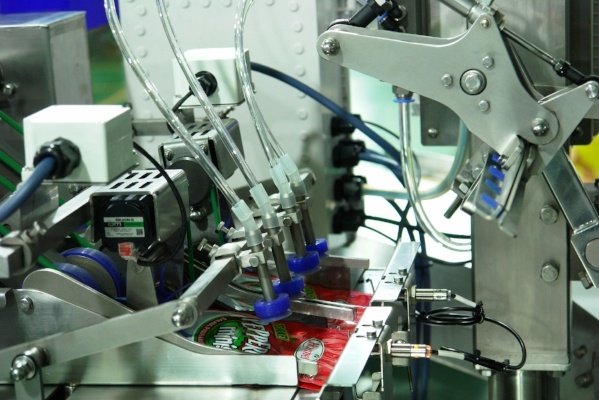
Final Thought
In conclusion, the value of quick and reliable packaging machine repair work services can not be overemphasized, as they play an important role in decreasing downtime and ensuring operational efficiency. Carrying out proactive upkeep methods and spending in personnel training additional boosts the durability of packaging equipment.
Prompt repairs of product packaging equipments are critical for keeping operational performance and decreasing downtime.Additionally, prompt repair work contribute to the durability of packaging machinery. On the whole, the advantages of involving trustworthy service providers expand beyond instant fixings, positively affecting the whole functional operations of packaging procedures.

Report this page